
AirBorn gets flexible in MilAero, medical, industrial design spaces
Stephen Law
Electronics Production / Materials Contract Manufacturing Engineering Medical Supply ChainToronto-based flexible circuit manufacturer delivers personalized support
Electronic designers looking for a supplier that demonstrates flexibility, might get more than expected when dealing with AirBorn Flexible Circuits Inc. (AFC), a Toronto-based developer of rugged connectors, custom assemblies and engineering services for defense, space, aerospace, medical and industrial applications.
Operating as Stratflex since the mid-1950s, the Toronto electronic assembler was purchased in 2008 by AirBorn Inc. – headquartered in Georgetown, Texas. Since then, the firm has been producing integrated component and flex circuit design solutions to a large base of North American and European customers. From initial CAD models to full-scale production, AirBorn guides the customer’s application through the design, prototyping, testing and qualifying process – before ramping into full scale production.

Source: Airborn
“We have expanded from the early days of just being a component supplier. We’ve taken that business model and grown it to include cable assemblies, flexible circuits and flex assemblies, all the way to complete box build integration,” says Billy Rhea, product director of embedded systems with AirBorn, based out of the firm’s HQ.
AFC develops many of its client’s designs using a wide range of connectors, terminations, components and devices, providing automatic and Mil-certified precision hand soldering. Some of the relevant military standards (MIL-STD) they typically adhere to include: MIL-PRF-31032; MIL-P-50884; MIL-STD-883; MIL-STD-202; MIL-STD-810; IPC-6013 and AS9100.
Approved vendors
“If a customer has an existing design, we can just build to their specification. If they need help designing, we can do that as well. We also conduct services that include manufacturability, repairability, reliability, and testability. We also help the customer create a bill of material (BOM) if they need it – especially If they don’t have approved vendors,” states Peter Pialis, Director of Engineering at the Toronto facility. “The customer literally just takes out the flex assembly, plugs it in, and they’re good to go.”
Primarily focused on applications relating to defense, space, aerospace, medical and industrial industries, AirBorn produces highly reliable, flexible, printed circuit and assembly solutions – single-sided, double-sided, multi-layer, rigid-flex and sculptured flex. The benefits of flex, is that it provides certain designs with a customizable solution for wire harnesses, including repeatability, consistency, and cost-effectiveness for high-volume orders.
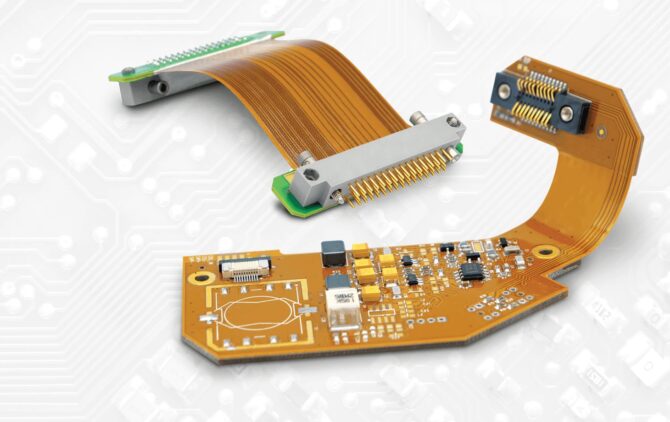
Source: Airborn
“Most people don’t understand what flex can do in their design, which is quite surprising. We recently hosted a lunch and learn for 20 design engineers and they were not aware of the benefits flexible circuits can bring to their design.” says Pialis.
Airborn also provides a full range of integrated services comprising design, DFm, DFt, prototypes, production manufacturing, hand and automated assembly, as well as testing. This also includes fully populated flexible circuit assembly (adding pcb components to the flex circuit). AirBorn will often add a flexible circuit into the customer’s finished product, sometimes as much as up to 100-feet long.
60% reduction in mass
“Integration of high-speed AirBorn connector product into our flex options has allowed customers to replace these big, heavy cable assemblies,” adds Rhea. “They’re using high-end twinax, coax type of cables that can be replicated in flexible circuits. We’re implementing that into a flex and sculpting it ― putting in whatever format they need. As a result, we’ve seen as much as 60% reduction in mass, which translates to a huge saving for them over space and weight. We’re getting great performance out of that flex, especially the military and space customers, and they are raving over it.”
AirBorn employs a team of product engineers, who conduct product realization ― from specifications to an actual manufactured product. The product development also leverages process engineers, led by electrical engineers, chemical engineers, and mechanical engineers.
“We’ve got multiple design engineers on staff to help with customer’s design applications. Some clients already have their Gerber files ready when they come through our door, others just want to know, ‘can we build it’,” notes Rhea.
Raw materials
AirBorn uses a variety of raw materials to produce flexible circuits, tailored to meet the specific needs of their customers. Some of the primary raw materials include:
- Polyimide Films: Kapton and Apolong;
- Copper Foils: Electro-deposited (ED) Copper and Rolled-Annealed (RA) Copper;
- Adhesives: Acrylic, Epoxy and Pressure-Sensitive Adhesives (PSAs);
- Coverlays: Polyimide Coverlays, and Flexible Solder Masks;
- Conductive Inks and Pastes: Dielectric, as well as Silver and Carbon Inks;
- Reinforcement Materials: Stiffeners and Bondplys;
- Protective Coatings: Conformal Coatings and encapsulants;
- Specialty Films and Laminates: PTFE (Teflon) Films, and Liquid Crystal Polymer (LCP) Films.
Supported by on-going investment in new equipment, AirBorn’s 37,000-sq ft production space boasts state-of-the-art automated optical inspection (AOI) systems; Laser cutting and drilling machines; Roll-to-roll processing equipment; Soldering and reflow ovens; Vacuum lamination presses; X-ray inspection systems; Etching and plating equipment; and Clean room facilities.
While 90% of the Toronto facility serves U.S.-based clients, AirBorn’s goal remains focused on increasing market share of home-grown design customers.
“Our biggest selling point is our design service capabilities, and our customer service,” Rhea concludes. “We are equipped to expand our business with the Canadian military market, based on our current success in the US as a second- or third-tier type supplier for players like Lockheed, Raytheon, BAE, and Boeing.”